When considering flooring options, a cement floor offers several advantages that make it an attractive choice for many homeowners and businesses. This durable and versatile material provides benefits that go beyond aesthetics, making it a practical option for various settings. Let’s explore the key advantages of installing a cement floor in your space.
Durability and Longevity
One of the most significant benefits of a cement floor is its durability. Concrete, the primary material in cement floors, is known for its strength and resilience. Concrete is an artificial composite material, comprising a matrix of cementitious binder (typically Portland cement paste or asphalt) and a dispersed phase or “filler” of aggregate (typically a rocky material, loose stones, and sand). The binder “glues” the filler together to form a synthetic conglomerate. Many types of concrete are available, determined by the formulations of binders and the types of aggregate used to suit the application of the engineered material. These variables determine strength and density, as well as chemical and thermal resistance of the finished product (excerpt from the website https://en.wikipedia.org/wiki/Concrete).
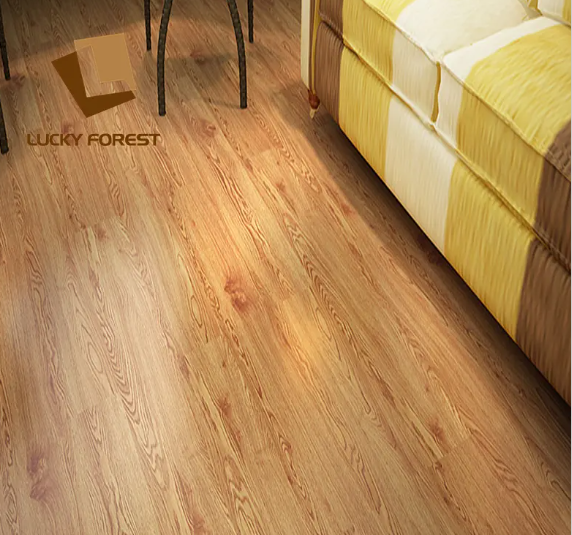
The robust nature of concrete ensures that a cement floor can withstand heavy foot traffic, furniture, and even machinery. This durability translates to a longer lifespan compared to other flooring materials. With proper maintenance, a cement floor can last for decades, making it a cost-effective investment in the long run.
Low Maintenance Requirements
Another advantage of a cement floor is its low maintenance requirements. Unlike carpets or wooden floors, which need regular cleaning and special treatments, a cement floor is relatively easy to care for. Regular sweeping and occasional mopping are usually sufficient to keep it clean. Additionally, cement floors are resistant to stains and spills, making them ideal for high-traffic areas or spaces prone to messes.
For those who prefer a low-maintenance flooring option, cement floors offer the perfect solution. They do not require waxing, polishing, or other time-consuming upkeep routines. This ease of maintenance not only saves time but also reduces the cost associated with floor care.
Versatility in Design
Cement floors are not just about functionality; they also offer versatility in design. Modern techniques allow for various finishes, colors, and patterns, enabling homeowners and designers to achieve the desired aesthetic. Whether you prefer a polished, glossy finish or a more rustic, textured look, cement floors can be customized to match your style.
Moreover, cement floors can be stained, stamped, or even embedded with decorative elements to create unique designs. This flexibility in design makes cement floors suitable for a wide range of settings, from industrial spaces to contemporary homes.
Environmental Benefits
Choosing a cement floor also contributes to environmental sustainability. Concrete is made from natural materials, and its production requires less energy compared to other flooring options. Additionally, cement floors have a long lifespan, which reduces the need for frequent replacements and the associated environmental impact.
Furthermore, cement floors can help improve indoor air quality. Unlike carpets, which can trap dust, allergens, and pollutants, cement floors provide a cleaner surface that does not harbor these harmful particles. This makes them an excellent choice for people with allergies or respiratory issues.
Cost-Effectiveness
When it comes to cost, cement floors offer an affordable option for both initial installation and long-term savings. The materials used in cement floors are relatively inexpensive, and the installation process is straightforward. Additionally, the durability and low maintenance of cement floors mean fewer repair and replacement costs over time.
For budget-conscious homeowners or businesses looking for a practical and stylish flooring option, cement floors provide excellent value for money.
Conclusion
A cement floor offers numerous advantages, including durability, low maintenance, design versatility, environmental benefits, and cost-effectiveness. These qualities make cement floors a popular choice for various applications, from residential to commercial settings. By choosing a cement floor, you invest in a flooring option that combines practicality with aesthetic appeal, ensuring long-term satisfaction.